3LPE – Three layer polyethylene
EXTERNAL COATING AND INTERNAL LINING
V.I.P. Pesaro is one of the few companies able to offer the 3LPE coating on pipes as well as on custom pieces.
The coating is a multilayer composed of a primer fusion bonded epoxy (FBE) followed by an adhesive copolymer and another layer of polyethylene which provides resistance and long-lasting protection.
The system ensures the applicability of the sintered coating also on pieces with special shapes.
Long-lasting corrosion protection
The FBE primer offers an excellent adhesion to the substrate and provides a long-term corrosion protection for pipelines operating at moderate temperatures.
It also ensures the resistance to the cathodic disbondment so the total cost of cathodic protection of the pipeline decreases.
Remarkable mechanical protection
The applied polyethylene layer protects the pipeline during shipping and installation reducing repair costs and providing an underground protection against mechanical, chemical and abrasive attacks.
Applying an higher polyethylene thickness the mechanical protection increases proportionally.
Advantages of the sintered system
V.I.P. Pesaro using this special application technique is able to coat also specific pieces with special shapes (bends, tees, reducers, joints, etc.).
There aren’t any limitations about the amount of pieces to coat, even the single piece can be treated.
3LPE can be applied in different thicknesses to meet the requirements of project specifications.
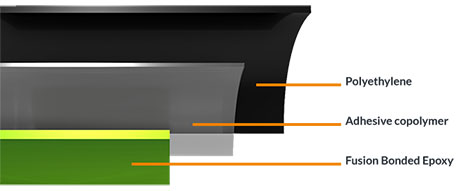
- Small and large pipes
- Standard and special fittings
- Wide radius bends
- Flanges
- Custom pieces
- Elongation at Break : > 600%
- Hardness : Shore D 52
- Minimum recommended temperature : – 40°C
- Maximum recommended temperature : + 80°C
- SURFACE PREPARATION : The steel surface is thoroughly cleaned and blasted.
- FUSION BONDED EPOXY – Anticorrosive coating* : The cleaned metal part is heated to the recommended FBE powder application temperature.
- ADHESIVE LAYER : A copolymer adhesive provides the necessary adhesion between the primer and the third layer of the coating.
- POLYETHYLENE – Top coat : The outer layer is made of a polyolefin protective film of Polyethylene (PE).
- SHIPMENT PREPARATION : Final inspection is carried out in our internal laboratory when the goods are fully produced. Then packed and in all respects ready for shipment.
*Sintering is the coating process where a coating powder is sprayed on a preheated piece. Thanks to the heat emitted from the surface the powder fuses creating an homogeneous and continuous layer.
FBE (Fusion Bonded Epoxy) is the best epoxy resin powder applied on pre‐heated surfaces. Thermosetting coating designed for the anticorrosive protection of articles destined to immersion or buried services in oil and gas sector and in the protection of the water pipeline.
3LPE PROCESS
EXTERNAL COATING
INTERNAL LINING
INSPECTION AND TESTING
Property | Test Description | Typical Values |
---|---|---|
Degree of cure of epoxy resin | DIN 30670 | ∆Tg according to the manufacturer specifications |
Impact | DIN 30670 | ≥ 7 J/mm |
Cathodic Disbondment | DIN 30670 | 23°C/ 28 days or 60°C/ 2 days max 7 mm |
Peel Strenght | DIN 30670 | 35 N/cm at 23°C; 15 N/cm at 70°C |
Continuity (holiday detection) | DIN 30670 | 10 kV/mm; max 25kV |
COATING CAPACITY
Pipes:
Diameter from 1/2” to 120”
Maximum unit length 13.5 meters
Maximum unit weight 15,000 kg.
Joints and/or custom pieces: (bends, tees, reducers, flanges, etc.)
Maximum size 3.0 x 3.0 x 13.5 meters
Maximum unit weight 15,000 kg
Maximum thickness of the coating 3,5 mm